Shippers and carriers depend, now more than ever, on collecting measurements accurately, quickly, and efficiently.
Shippers and carriers need a way to verify and control invoices that directly impact profit and loss.
With the implementation of a pallet dimensioner in their operations – a tool that retrieves the dimensional data (length, width, and height) of the pallet – shippers and carriers can avoid costly dimensional errors and incorrect invoicing.
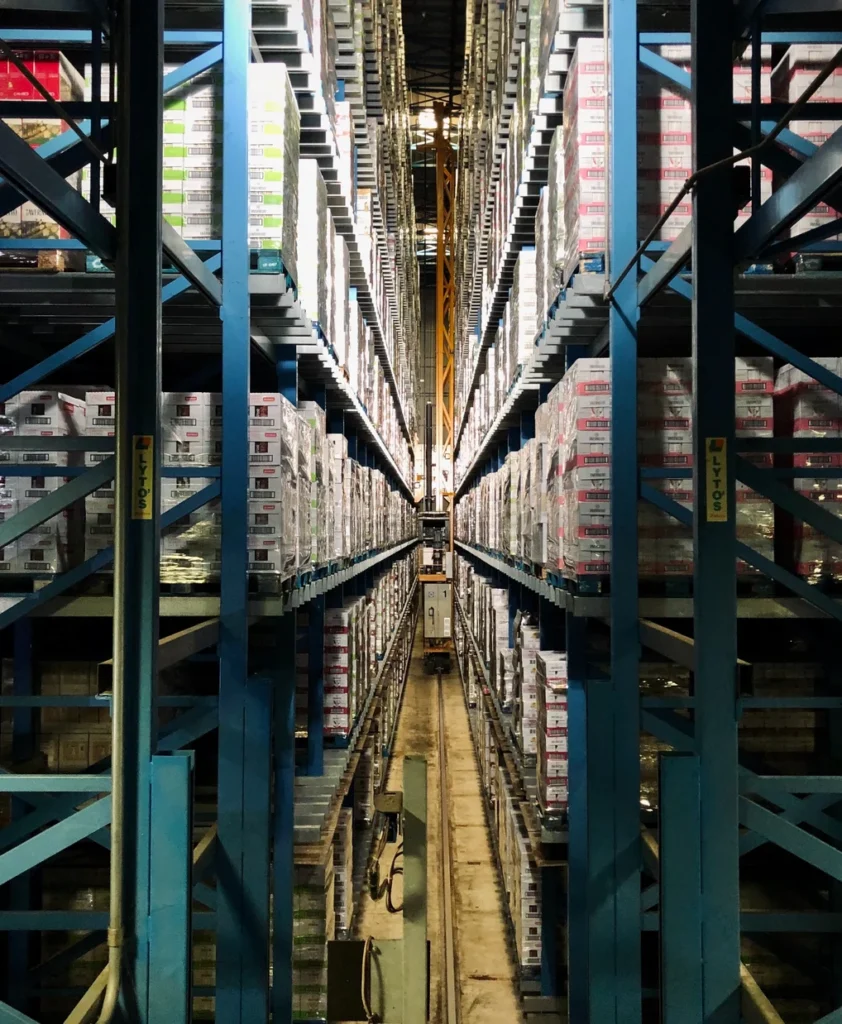
Reasons For Dimensioning
1. Accurate invoices
Both shippers and carriers need a control mechanism for correct and exact delivery measurements and weights.
This control mechanism is dimensioning which ensures that invoices (or freight bills of lading) have accurate information about the dimensional weight of the shipped or received goods.
From the shippers’ point of view the importance of dimensioning lies in knowing the exact measurements and weight of each pallet in the warehouse in order to have proof (or transport invoice control) for carriers that the dimensions for the shipped product are accurate in case of false volumetric surcharges, which otherwise could not be refuted without the necessary documentation.
From the carriers’ point of view, the importance of dimensioning is to verify that the shipper has shipped the product with the exact measurements and weight they claim. This helps to provide accurate invoices and ensures that the carrier does not have to transport more volumetric weight than the carrier is supposed to. Correct dimensions directly impact their P&L.
Accurate dimensional data increases the accuracy of the information provided in invoices, making sure customers do not overpay for dimensions they did not pay for.
Parcel, LTL (Less-Than-Truckload), and groupage carriers invoice their customers based on the weight and dimensional weight of the items. Therefore, dimensioning is a crucial process in their business. Every mistake in the process has a direct impact on the profits and loss and profit margin.
2. Quality control
Goods can get damaged during transport, but since automated dimensioning systems can take an image of the products – either of a pallet or a box – shippers can provide proof that the packaging was in perfect condition before transport. In that case, the discussion arises if the goods were damaged before or during shipping. With a picture and a timestamp, you can protect yourself as a shipper. 3. Space utilization and slotting
In warehouse and fulfillment processes money translates to space and vice versa, so having the data for precise dimensional information of your product is crucial.
With an automated dimensioning system, pallet dimensions can be automatically imported into a warehouse management system (WMS) or transport management system (TMS) which simplifies the process of determining how and where to arrange products for optimized pick density and decreased order fulfillment time, by considering the size of the available warehouse slots and Ti-Hi.
For example, during inbound deliveries, the inbound pallets need to be positioned in a warehouse slot. The possible slots depend on the height of the pallet and the size of the slot. Therefore, you need to know the current availability of your warehouse slots, whether they can be stacked on top of other pallets due to the weight, and many other slotting criteria.
Dimensioning methods
There are two main types of dimensioning methods – traditional (or manual) dimensioning and automated dimensioning.
Traditional dimensioning means the manual way of measuring and weighing the product. This process entails measuring pallets with a tape measurer and then entering this data into a WMS or TMS.
Automated dimensioning entails measuring the same dimensions by using a dimensioner – a machine paired with cameras and a weighing scale to calibrate the dimensional weight (DIM) of items quicker and more accurately.